Forma strukturalna Usługa formowania wtryskowego online formy i jakość obróbki form bezpośrednio wpływają na jakość produktów z tworzyw sztucznych i wydajność produkcji. Najczęstsze i najczęściej występujące wady form w produkcji form wtryskowych i produktów z tworzyw sztucznych oraz ich główne przyczyny są analizowane i eliminowane w następujący sposób.
1. Trudności w usunięciu wlewu. Podczas procesu formowania wtryskowego wlew przykleja się do tulei wlewu i niełatwo go usunąć. Po otwarciu formy na produkcie pojawiają się pęknięcia i uszkodzenia. Ponadto operator musi wybić go z dyszy końcówką miedzianego pręta, aby poluzować go przed wyjęciem z formy, co poważnie wpływa na wydajność produkcji. Główną przyczyną tej awarii jest słabe wykończenie otworu stożkowego wlewu i ślady po nożu w kierunku obwodowym otworu wewnętrznego. Po drugie, materiał jest zbyt miękki, a mały koniec otworu stożkowego ulega deformacji lub uszkodzeniu po pewnym czasie użytkowania, a sferyczna krzywizna dyszy jest zbyt mała, co powoduje, że materiał wlewu wytwarza tutaj łeb nitu. Otwór stożkowy wlewu jest trudny w obróbce i należy w jak największym stopniu używać standardowych części. Jeśli musisz sam go przetworzyć, powinieneś również wykonać lub kupić specjalny rozwiertak. Otwór stożkowy należy zeszlifować do Ra0,4 lub wyższej. Dodatkowo należy zamontować drążek bramy lub mechanizm wyrzucający bramę.
2. Uszkodzenie sworznia prowadzącego. Sworzeń prowadzący pełni rolę prowadzącą w formie, aby zapewnić, że powierzchnie formowania rdzenia i wnęki nie zderzą się ze sobą w żadnych okolicznościach. Sworzeń prowadzący nie może być używany jako część przenosząca siłę lub część pozycjonująca. W następujących przypadkach formy dynamiczne i stałe będą generować ogromne siły przesunięcia bocznego podczas wtrysku: (1). Gdy wymagania dotyczące grubości ścianki części z tworzywa sztucznego są nierówne, natężenie przepływu materiału przez grubą ściankę jest duże i tutaj generowane jest duże ciśnienie; (2). Bok części z tworzywa sztucznego jest asymetryczny, np. przeciwciśnienie po dwóch przeciwległych stronach formy ze schodkową powierzchnią podziału nie jest równe.
3. Duże formy będą wytwarzać dynamiczne i stałe przesunięcia formy ze względu na różne szybkości napełniania we wszystkich kierunkach i wpływ własnego ciężaru formy podczas instalacji formy. W powyższych przypadkach siła przesunięcia bocznego zostanie dodana do sworznia prowadzącego podczas wtrysku, a powierzchnia sworznia prowadzącego zostanie zgrubiona i uszkodzona po otwarciu formy. W poważnych przypadkach sworzeń prowadzący wygnie się lub zostanie odcięty, a nawet formy nie będzie można otworzyć. Aby rozwiązać powyższe problemy, po każdej stronie powierzchni rozdzielającej formę dodawane są klucze pozycjonujące o dużej wytrzymałości. Najprostszym i najskuteczniejszym sposobem jest użycie kluczy cylindrycznych. Pionowość otworu sworznia prowadzącego i powierzchni rozdzielającej ma kluczowe znaczenie. Podczas przetwarzania formy dynamiczne i stałe są wyrównywane i zaciskane, a następnie rozwiercane jednorazowo na wytaczarce. Zapewnia to koncentryczność otworów formy dynamicznej i stałej oraz minimalizuje błąd pionowości. Ponadto twardość obróbki cieplnej sworzni prowadzących i tulei prowadzących musi spełniać wymagania projektowe.
4. Dynamiczny szablon jest wygięty. Podczas wtrysku formy, stopiony plastik w gnieździe formy generuje ogromne przeciwciśnienie, zazwyczaj 600 ~ 1000 kg/cm. Producenci form czasami nie zwracają uwagi na ten problem, często zmieniając oryginalny rozmiar projektu lub zastępując dynamiczny szablon płytą stalową o niskiej wytrzymałości. W formie z popychaczem, duża rozpiętość dwóch bocznych gniazd powoduje, że szablon wygina się podczas wtrysku. Dlatego dynamiczny szablon musi być wykonany z wysokiej jakości stali o wystarczającej grubości. Nie wolno używać płyt stalowych o niskiej wytrzymałości, takich jak A3. W razie potrzeby należy ustawić kolumnę podporową lub blok podporowy pod dynamicznym szablonem, aby zmniejszyć grubość szablonu i poprawić nośność.
5. Popychacz jest wygięty, złamany lub przecieka. Jakość samodzielnie wykonanego wyrzutnika jest dobra, ale koszt obróbki jest zbyt wysoki. Obecnie powszechnie stosuje się standardowe części, a ich jakość jest słaba. Jeśli szczelina między wyrzutnikiem a otworem jest zbyt duża, nastąpi wyciek, ale jeśli szczelina jest zbyt mała, wyrzutnik rozszerzy się i utknie z powodu wzrostu temperatury formy podczas wtrysku. Co jest bardziej niebezpieczne, czasami wyrzutnika nie można wypchnąć poza ogólną odległość i pęka. W rezultacie odsłoniętego wyrzutnika nie można zresetować podczas następnego zamykania formy i uderza on w matrycę. Aby rozwiązać ten problem, wyrzutnik jest ponownie szlifowany, a na przednim końcu wyrzutnika zostaje zachowana pasująca sekcja o grubości 10-15 mm, a środkowa część jest szlifowana o 0,2 mm. Po zmontowaniu należy dokładnie sprawdzić, czy wszystkie wyrzutniki mają odpowiedni luz, który zazwyczaj mieści się w granicach 0,05–0,08 mm. Ma to na celu zapewnienie swobodnego ruchu całego mechanizmu wyrzutnika do przodu i do tyłu.
6. Słabe chłodzenie lub wyciek wody. Efekt chłodzenia formy bezpośrednio wpływa na jakość i wydajność produkcji produktu. Na przykład słabe chłodzenie spowoduje duże kurczenie się produktu lub nierównomierne kurczenie się, odkształcanie i deformację. Z drugiej strony, jeśli forma zostanie przegrzana w całości lub w części, nie można jej normalnie uformować i produkcja zostaje zatrzymana. W poważnych przypadkach wyrzutnik i inne ruchome części ulegają uszkodzeniu z powodu rozszerzalności cieplnej i zacinania. Konstrukcja i przetwarzanie układu chłodzenia są określone przez kształt produktu. Nie pomijaj tego układu, ponieważ struktura formy jest złożona lub przetwarzanie jest trudne. W szczególności duże i średnie formy muszą w pełni uwzględniać problem chłodzenia.
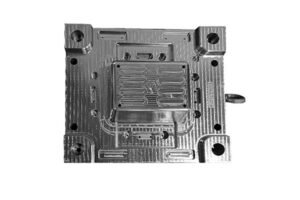
7. Mechanizm napinający o stałej odległości ulega awarii. Mechanizmy napinające o stałej odległości, takie jak haki wahadłowe i klamry, są zazwyczaj stosowane w stałym wyciąganiu rdzenia formy lub niektórych formach wtórnego wyjmowania z formy. Ponieważ mechanizmy te są ustawione parami po obu stronach formy, ich ruchy muszą być zsynchronizowane, to znaczy forma jest zamykana, a klamra zwalniana w tym samym czasie, a forma jest otwierana do określonej pozycji i odczepiana w tym samym czasie. Po utracie synchronizacji szablon wyciągniętej formy nieuchronnie zostanie przekrzywiony i uszkodzony. Części tych mechanizmów muszą mieć większą sztywność i odporność na zużycie, a regulacja jest również trudna. Żywotność mechanizmu jest krótka. Staraj się ich unikać i zamiast tego używaj innych mechanizmów. Gdy siła wyciągania rdzenia jest stosunkowo niewielka, można zastosować metodę sprężynowego wypychania stałej formy. Gdy siła wyciągania rdzenia jest stosunkowo duża, rdzeń może się ślizgać, gdy ruchoma forma się wycofuje. Można zastosować strukturę polegającą na najpierw zakończeniu działania wyciągania rdzenia, a następnie oddzieleniu formy. W przypadku dużych form można użyć hydraulicznego cylindra do wyciągania rdzenia. Mechanizm wyciągania rdzenia typu suwaka ze skośnym sworzniem jest uszkodzony. Najczęstsze problemy tego mechanizmu to głównie nieodpowiednia obróbka i zbyt małe materiały. Istnieją głównie dwa następujące problemy. Zaletą dużego kąta pochylenia sworznia A jest to, że może on wytworzyć większą odległość wyciągania rdzenia w krótszym skoku otwierania formy. Jednakże, jeśli kąt pochylenia A jest zbyt duży, gdy siła wyciągania F ma określoną wartość, siła zginająca P=F/COSA na pochylonym sworzniu podczas procesu wyciągania rdzenia jest również większa, a pochylony sworzeń jest podatny na odkształcenia i zużycie pochylonego otworu. Jednocześnie, skierowany w górę nacisk N=FTGA generowany przez pochylony sworzeń na suwaku jest również większy. Ta siła zwiększa dodatnie ciśnienie suwaka na powierzchni prowadzącej w rowku prowadzącym, zwiększając tym samym opór tarcia podczas przesuwania suwaka. Łatwo jest spowodować nierównomierne przesuwanie i zużycie rowka prowadzącego. Doświadczenie pokazuje, że kąt nachylenia A nie powinien być większy niż 25
8. Niektóre formy są ograniczone przez obszar szablonu. Długość rowka prowadzącego jest zbyt mała, a suwak jest odsłonięty poza rowkiem prowadzącym po zakończeniu czynności wyciągania rdzenia. To łatwo spowoduje przechylenie suwaka na etapie wyciągania rdzenia po zakończeniu i na początkowym etapie zamykania i resetowania formy. Zwłaszcza gdy forma jest zamknięta, suwak nie jest resetowany płynnie, co powoduje uszkodzenie suwaka lub nawet jego wygięcie. Zgodnie z doświadczeniem długość suwaka pozostawionego w rowku ślizgowym po zakończeniu czynności wyciągania rdzenia nie powinna być mniejsza niż 2/3 całkowitej długości rowka prowadzącego.
9. Na koniec, projekt. Podczas produkcji formy, powinna ona być oparta na konkretnych warunkach, takich jak wymagania jakościowe części z tworzywa sztucznego, wielkość partii i wymagania okresu produkcji. Może nie tylko spełniać wymagania produktu, ale także być najprostsza i najbardziej niezawodna w strukturze formy, łatwa w obróbce i tania. Jest to najdoskonalsza forma.