플라스틱 사출 성형 오버몰딩 콜드 러너는 금형 입구와 제품 게이트 사이의 부분을 말합니다. 러너의 플라스틱은 사출 압력과 자체 열에 의해 흐릅니다. 러너는 성형 재료의 일부이지만 제품에 속하지 않습니다. 따라서 금형을 설계할 때 충전 효과와 러너를 단축하고 줄여 재료를 절약하는 방법을 모두 고려해야 합니다. 이는 이상적인 상황이지만 실제 응용 프로그램에서 두 가지의 장점을 모두 얻는 것은 어렵습니다.
핫 러너(Hot runner)는 논 러너(non-runner)라고도 하며, 러너의 플라스틱이 각 주입 후 응고되지 않고, 플라스틱 제품을 탈형할 때 러너의 물 배출구를 제거할 필요가 없음을 의미합니다. 러너의 플라스틱이 응고되지 않기 때문에 다음 주입 시에도 러너가 여전히 방해받지 않습니다.
간단히 말해서, 핫 러너는 사출성형기 노즐의 확장 장치입니다.
핫 러너 몰드는 오늘날 세계의 산업적으로 발달된 국가와 지역에서 널리 사용되고 있습니다. 이는 주로 핫 러너 몰드가 다음과 같은 중요한 특징을 가지고 있기 때문입니다.
부품의 성형주기 단축
러너 시스템에는 냉각 시간 제한이 없으므로 성형 및 경화 후 부품을 제 시간에 꺼낼 수 있습니다. 핫 러너 몰드로 생산된 많은 얇은 벽 부품의 성형 주기는 5초 미만일 수 있습니다.
플라스틱 원료를 절약하세요
순수한 핫 러너 몰드에서는 콜드 러너가 없기 때문에 생산 비용이 없습니다. 이는 플라스틱이 비싼 응용 분야에서 특히 중요합니다. 사실, 주요 국제 핫 러너 제조업체는 세계에서 석유와 플라스틱 원료가 비싼 시대에 빠르게 발전했습니다. 핫 러너 기술은 재료 비용을 줄이고 재료 비용을 줄이는 효과적인 방법이기 때문입니다.
낭비를 줄이고 제품 품질을 향상시키세요
핫 러너 금형 성형 공정 동안 플라스틱 용융물의 온도는 러너 시스템에서 정확하게 제어됩니다.
플라스틱은 각 금형 캐비티에 더 균일한 상태로 유입되어 일관된 품질의 부품을 생산할 수 있습니다. 핫 러너 성형 부품의 게이트 품질이 좋고, 탈형 후 잔류 응력이 낮으며, 부품의 변형이 작습니다. 따라서 시중에 나와 있는 많은 고품질 제품은 핫 러너 금형으로 생산됩니다.
이후의 프로세스를 없애면 생산 자동화에 도움이 됩니다.
핫 러너 금형이 형성된 후, 제품은 완제품이며, 게이트를 트리밍하고 콜드 러너를 재활용할 필요가 없습니다. 생산 자동화에 도움이 됩니다. 많은 외국 제품 제조업체가 핫 러너를 자동화와 결합하여 생산 효율성을 크게 개선합니다.
사출성형 공정의 적용범위 확대
많은 고급 플라스틱 성형 공정이 핫 러너 기술을 기반으로 개발되었습니다. 예를 들어 PET 사전 성형, 금형 내 다색 공동 사출, 다중 재료 공동 사출 공정 등이 있습니다.
핫 러너 몰드는 콜드 러너 몰드에 비해 많은 상당한 장점이 있지만 몰드 사용자는 핫 러너 몰드의 단점도 이해해야 합니다. 요약하면 다음과 같은 사항이 있습니다.
곰팡이 비용 상승
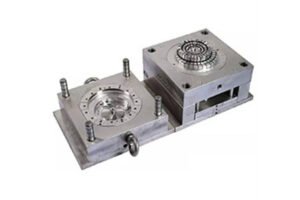
핫 러너 구성 요소는 비교적 비싸고 핫 러너 금형의 비용이 상당히 증가할 수 있습니다. 부품 출력이 작으면 금형 도구 비용 비율이 높고 경제적으로 가치가 없습니다. 많은 개발도상국의 금형 사용자에게 핫 러너 시스템의 높은 가격은 핫 러너 금형의 광범위한 사용에 영향을 미치는 주요 문제 중 하나입니다.
핫러너 금형 제조 공정 장비에 대한 높은 요구 사항
핫 러너 금형은 정밀 가공 기계가 필요합니다. 핫 러너 시스템과 금형 간의 통합 및 매칭 요구 사항은 매우 엄격합니다. 그렇지 않으면 금형은 생산 과정에서 많은 심각한 문제를 겪게 됩니다. 예를 들어, 플라스틱 밀봉이 불량하면 플라스틱 오버플로가 발생하고 핫 러너 구성 요소가 손상되어 생산이 중단되고 노즐 인서트와 게이트 사이의 상대 위치가 불량하면 제품 품질이 심각하게 저하됩니다.
복잡한 운영 및 유지 관리
콜드 러너 몰드와 비교했을 때 핫 러너 몰드는 작동 및 유지 관리가 복잡합니다. 부적절한 작동을 사용하면 핫 러너 부품이 손상되기 매우 쉽고 생산이 불가능하며 막대한 경제적 손실을 초래합니다. 핫 러너 몰드를 처음 사용하는 경우 사용 경험을 축적하는 데 오랜 시간이 걸립니다.