Plastic Contract Manufacturing Companies Plastic Injection Molding Defects: Causes and Solutions
Filling Defects
Filling defects often result in incomplete filling or edge collapse, leading to defective products, wasted material, labor, and time. Possible causes include:Nozzle Temperature: Too low
Material Supply: Insufficient
Flowability: Poor
Injection Pressure: Too low
Gate: Too small or incorrectly positioned
Mold Surface: Not smooth enough
Nozzle: Blocked
Venting: Inadequate
Flash or Burr
Flash or burr typically occurs at the parting line and can complicate machining, distort the part, or even cause defects. Possible causes include:
Nozzle Temperature: Too high
Material Injection: Excessive
Flowability: Excellent
Injection Pressure: Too high
Clamping Force: Insufficient
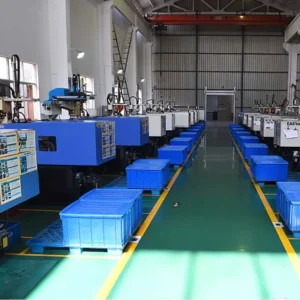
Sink Marks
Sink marks are caused by material shrinkage after injection molding. Possible causes include:
Nozzle Temperature: Too high
Resin Supply: Insufficient
Shrinkage: Excessive
Injection Molding Pressure: Too low
Holding Time: Too short
Injection Speed: Too slow
Mold Temperature: Too high
Cooling Time: Too short
Product Thickness: Uneven
Gate: Too small
Welding Lines
Welding lines often occur in products with holes or complex shapes. Possible causes include:
Nozzle Temperature: Too low
Material: Insufficiently dried
Injection Speed: Too slow
Gate: Too small
Venting: Poor
Injection Pressure: Too low
As we can see, the types and causes of plastic injection molding defects are influenced by a combination of factors. These include the performance of the molding machines, the characteristics of the molding materials, mold design and materials, filling control systems, and various operating processes. Despite rapid advancements in injection molding technology and its relative maturity, controlling defects remains increasingly challenging. This requires the use of advanced theories and technologies to reduce and eliminate injection molding defects effectively.