Pièces en plastique pour automobiles, telles que squelettes de bobines, bases, boîtes à fusibles, supports de lampe, fusibles à lame, boîtes de distribution centrale, gaines, crémaillères de poussée, moulage par injection de la console centrale Les pièces en plastique et les revêtements extérieurs sont principalement moulés par injection. Étant donné que ces pièces en plastique ont une grande précision de conception, le moulage par injection conventionnel ne peut pas être utilisé pour ces pièces en plastique, mais une technologie de moulage par injection de précision doit être utilisée. Afin de garantir les performances, la qualité et la fiabilité des pièces en plastique de précision pour l'automobile et de produire des produits en plastique de haute qualité qui répondent aux exigences de conception des produits, les matières plastiques, les équipements de moulage par injection, les moules et les processus de moulage par injection doivent être continuellement améliorés.
1. Principaux facteurs affectant le moulage par injection de précision La base pour déterminer le moulage par injection de précision est la précision du produit moulé par injection, c'est-à-dire la tolérance dimensionnelle, la tolérance de forme et de position et la rugosité de surface du produit. Il doit y avoir de nombreuses conditions liées au moulage par injection de précision, et les plus essentielles sont les quatre facteurs de base des matières plastiques, des moules d'injection, des processus de moulage par injection et de l'équipement de moulage par injection. Lors de la conception de produits en plastique, les matières plastiques techniques doivent être sélectionnées en premier, et les plastiques techniques qui peuvent être injectés avec précision doivent être sélectionnés parmi ceux qui ont des propriétés mécaniques élevées, une stabilité dimensionnelle, une bonne résistance au fluage et une résistance à la fissuration sous contrainte environnementale. Deuxièmement, la machine de moulage par injection appropriée doit être sélectionnée en fonction du matériau plastique sélectionné, de la précision de la taille du produit fini, du poids de la pièce, des exigences de qualité et de la structure de moule attendue. Dans le processus de traitement, les facteurs affectant les produits moulés par injection de précision proviennent principalement de la précision du moule, du retrait par injection et de la plage de variation de température et d'humidité ambiantes du produit. Dans le moulage par injection de précision, le moule est l'une des clés pour obtenir des produits en plastique de précision qui répondent aux exigences de qualité. Le moule utilisé pour le moulage par injection de précision doit répondre aux exigences de taille, de précision et de forme du produit. Cependant, même si la précision et la taille du moule sont cohérentes, la taille réelle du produit en plastique moulé sera incohérente en raison de la différence de retrait. Par conséquent, il est très important de contrôler efficacement le taux de retrait des produits en plastique dans la technologie de moulage par injection de précision. Que la conception du moule soit raisonnable ou non affectera directement le taux de retrait des produits en plastique. Étant donné que la taille de la cavité du moule est obtenue en ajoutant le taux de retrait estimé à la taille du produit en plastique, et que le taux de retrait est une valeur dans une plage recommandée par le fabricant de plastique ou le manuel des plastiques techniques, il n'est pas seulement lié à la forme de la porte, à la position de la porte et à la distribution du moule, mais également à l'orientation cristalline (anisotropie) du plastique technique, à la forme, à la taille, à la distance et à la position du produit en plastique par rapport à la porte. Les principaux facteurs qui affectent le taux de retrait des plastiques sont le retrait thermique, le retrait par changement de phase, le retrait d'orientation, le retrait par compression et la récupération élastique, et ces facteurs sont liés aux conditions de moulage ou aux conditions de fonctionnement des produits moulés par injection de précision. Par conséquent, lors de la conception du moule, il est nécessaire de prendre en compte la relation entre ces facteurs et les conditions de moulage par injection et leurs facteurs apparents, tels que la pression d'injection, la pression de la cavité et la vitesse de remplissage, la température de fusion par injection et la température du moule, la structure du moule et la forme et la distribution de la porte, ainsi que l'influence de facteurs tels que la section transversale de la porte, l'épaisseur de la paroi du produit, la teneur en charges de renforcement dans les matières plastiques, la cristallinité et l'orientation des matières plastiques. L'influence des facteurs ci-dessus varie également en fonction de la matière plastique, d'autres conditions de moulage telles que la température, l'humidité, la cristallisation continue, la contrainte interne après moulage et les changements dans la machine de moulage par injection. Étant donné que le processus de moulage par injection est le processus de transformation du plastique de solide (poudre ou granulaire) en liquide (fusion) puis en solide (produit). De la pastille à la masse fondue, puis de la masse fondue au produit fini, le processus doit passer par les effets du champ de température, du champ de contrainte, du champ d'écoulement et du champ de densité. Sous l'action conjointe de ces champs, différents plastiques (thermodurcissables ou thermoplastiques, cristallins ou non cristallins, renforcés ou non renforcés, etc.) ont des formes structurelles de polymère et des propriétés rhéologiques différentes. Tout facteur qui affecte les « champs » ci-dessus affectera inévitablement les propriétés physiques et mécaniques, la taille, la forme, la précision et la qualité d'apparence des produits en plastique. De cette façon, le lien inhérent entre les facteurs de processus et les performances du polymère, la forme structurelle et les produits en plastique se manifestera à travers les produits en plastique. L'analyse claire de ces liens inhérents est d'une grande importance pour formuler rationnellement le processus de moulage par injection, concevoir et fabriquer rationnellement les moules selon les plans, et même sélectionner rationnellement l'équipement de moulage par injection. Le moulage par injection de précision est également différent du moulage par injection ordinaire en termes de pression d'injection et de taux d'injection. Le moulage par injection de précision utilise souvent une injection à haute pression ou à ultra-haute pression et une injection à grande vitesse pour obtenir un taux de retrait de moulage plus faible. Compte tenu des raisons susmentionnées, en plus de prendre en compte les éléments de conception des moules généraux, les points suivants doivent également être pris en compte lors de la conception de moules d'injection de précision : ① Utiliser des tolérances de taille de moule appropriées ; ② Éviter les erreurs de retrait de moulage ; ③ Éviter la déformation par injection ; ④ Éviter la déformation par démoulage ; ⑤ Minimiser les erreurs de fabrication du moule ; ⑥ Éviter les erreurs de précision du moule ; ⑦ Maintenir la précision du moule.
2. Prévenir les erreurs de retrait de moulage Étant donné que le taux de retrait varie en raison de la pression d'injection, pour les moules à empreinte unique, la pression de la cavité dans la cavité doit être aussi constante que possible ; quant aux moules à empreintes multiples, la pression de la cavité entre les cavités doit être très faible. Dans le cas d'une cavité unique avec plusieurs portes ou de plusieurs cavités avec plusieurs portes, la même pression d'injection doit être injectée pour rendre la pression de la cavité constante. À cette fin, il est nécessaire de s'assurer que la position de la porte est équilibrée. Afin de rendre la pression de la cavité dans la cavité constante, il est préférable de maintenir la pression à l'entrée de la porte constante. L'équilibre de la pression à la porte est lié à la résistance à l'écoulement dans le canal d'écoulement. Par conséquent, avant que la pression de la porte ne soit équilibrée, le débit doit être équilibré. Étant donné que la température de fusion et la température du moule affectent le taux de retrait réel, lors de la conception de la cavité du moule d'injection de précision, afin de faciliter la détermination des conditions de moulage, une attention particulière doit être accordée à la disposition de la cavité. Étant donné que le plastique fondu apporte de la chaleur dans le moule, et que la distribution du gradient de température du moule est généralement autour de la cavité, sous la forme de cercles concentriques centrés sur le canal principal, des mesures de conception telles que l'équilibre des canaux d'écoulement, la disposition des cavités et la disposition concentrique centrée sur le canal principal sont nécessaires pour réduire l'erreur de retrait entre les cavités, élargir la plage admissible des conditions de moulage et réduire les coûts. La disposition des cavités du moule d'injection de précision doit répondre aux exigences d'équilibre des canaux d'écoulement et de disposition centrée sur le canal principal, et la méthode de disposition des cavités avec le canal principal comme ligne de symétrie doit être adoptée, sinon elle entraînera des différences dans les taux de retrait des différentes cavités. Étant donné que la température du moule a une grande influence sur le taux de retrait du moulage, elle affecte également directement les propriétés mécaniques du produit moulé par injection et provoque divers défauts de moulage tels que la surface fleurie du produit. Par conséquent, le moule doit être maintenu dans la plage de température spécifiée et la température du moule ne doit pas changer avec le temps. La différence de température entre les cavités du moule multi-empreintes ne doit pas changer. Pour cette raison, des mesures de contrôle de la température pour le chauffage ou le refroidissement du moule doivent être prises lors de la conception du moule, et afin de minimiser la différence de température entre les cavités du moule, une attention particulière doit être accordée à la conception du circuit de contrôle de la température et de refroidissement. Dans le circuit de contrôle de la température de la cavité et du cœur, il existe principalement deux méthodes de connexion : le refroidissement en série et le refroidissement en parallèle. Du point de vue de l'efficacité de l'échange thermique, le débit de l'eau de refroidissement doit être turbulent. Cependant, dans le circuit de refroidissement parallèle, le débit dans un circuit qui devient une dérivation est plus petit que le débit dans le circuit de refroidissement en série, ce qui peut former un flux laminaire, et le débit réel entrant dans chaque circuit peut ne pas être le même. Étant donné que la température de l'eau de refroidissement entrant dans chaque circuit est la même, la température de chaque cavité doit également être la même, mais en fait, en raison des différents débits dans chaque circuit et de la capacité de refroidissement différente de chaque circuit, la température de chaque cavité ne peut pas être constante. L'inconvénient de l'utilisation d'un circuit de refroidissement en série est que la résistance à l'écoulement de l'eau de refroidissement est importante et que la température de l'eau de refroidissement à l'entrée de la cavité avant est considérablement différente de la température de l'eau de refroidissement à l'entrée de la dernière cavité. La différence de température entre l'entrée et la sortie de l'eau de refroidissement varie en fonction de la taille du débit. Pour les petits moules d'injection de précision destinés au traitement de pièces en plastique pour automobiles, il est généralement plus approprié d'utiliser un circuit de refroidissement en série afin de réduire les coûts de moulage. Si les performances de l'instrument de contrôle de la température du moule (machine) utilisé peuvent contrôler le débit d'eau de refroidissement à moins de 2 °C, la différence de température maximale de chaque cavité peut également être maintenue à moins de 2 °C. La cavité du moule et le noyau doivent avoir leur propre système de circuit d'eau de refroidissement. Dans la conception du circuit de refroidissement, en raison de l'apport de chaleur différent de la cavité et du noyau, la résistance thermique de la structure du circuit est également différente et la température de l'eau à l'entrée de la cavité et du noyau aura une grande différence de température. Si le même système est utilisé, la conception du circuit de refroidissement est également difficile. Les noyaux des petits moules d'injection utilisés pour les pièces en plastique automobiles générales sont très petits et il est très difficile d'utiliser des systèmes d'eau de refroidissement. Si possible, le noyau peut être en bronze et le noyau en bronze au béryllium solide peut être refroidi par refroidissement par insert. De plus, lors de la prise de mesures pour empêcher la déformation des produits moulés par injection, il est également espéré qu'une certaine différence de température entre la cavité et le noyau puisse être maintenue. Par conséquent, lors de la conception des circuits de refroidissement de la cavité à jus et du noyau, la température doit être réglée et contrôlée séparément.
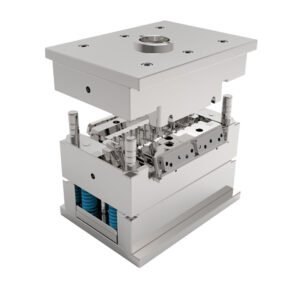
3. Maintien de la précision du moule du fabricant de pièces en plastique automobile Afin de maintenir la précision du moule sous la pression d'injection et la force de serrage, la faisabilité du meulage, du meulage et du polissage des pièces de cavité doit être prise en compte lors de la conception de la structure du moule. Bien que le traitement de la cavité et du noyau ait atteint les exigences de haute précision et que le taux de retrait soit le même que prévu, en raison du décalage central pendant le moulage, les dimensions pertinentes de l'intérieur et de l'extérieur des produits moulés sont difficiles à répondre aux exigences de conception des pièces en plastique. Afin de maintenir la précision dimensionnelle des cavités de modèle mobiles et fixes sur la surface de séparation, en plus du réglage de la colonne de guidage et du centrage du manchon de guidage couramment utilisés dans les moules conventionnels, il est également nécessaire d'ajouter des paires de positionnement telles que des broches de positionnement coniques ou des blocs de cales pour assurer une précision de positionnement précise et fiable. Le matériau de fabrication des moules d'injection de précision doit être un acier à outils allié de haute qualité avec des propriétés mécaniques élevées et un faible fluage thermique. Le matériau du moule pour la fabrication des cavités et des canaux doit être sélectionné avec une dureté élevée, une bonne résistance à l'usure, une forte résistance à la corrosion et une résistance à la déformation thermique après un traitement thermique strict. Dans le même temps, la difficulté et l'économie du traitement mécanique et du traitement électrique doivent également être prises en compte. Afin d'éviter que la précision dimensionnelle du moule ne change en raison du vieillissement, il est nécessaire de spécifier le traitement de revenu ou le traitement à basse température de la structure austénitique résiduelle du matériau du moule pendant le traitement thermique lors de la conception du moule. Pour les parties vulnérables des moules d'injection de précision, en particulier la cavité, le noyau et d'autres parties vulnérables, la possibilité de réparation doit être envisagée lors de la conception afin de maintenir la haute précision du moule après réparation.
IV. Conclusion La technologie de moulage par injection de précision est la technologie de production principale et clé pour les pièces en plastique automobile, et la conception de moules d'injection de précision est la partie principale de cette technologie de production. Une conception raisonnable de moules d'injection de précision est la base et la condition préalable nécessaire pour obtenir des produits de précision. En déterminant raisonnablement la taille et la tolérance du moule, en prenant des mesures techniques pour éviter les erreurs de retrait, la déformation par injection, la déformation par démoulage, le débordement, etc. des produits moulés par injection, et en garantissant la précision du moule, et en utilisant le processus de moulage par injection de précision correct, les matières plastiques techniques applicables et l'équipement de moulage par injection de précision pour obtenir la meilleure correspondance, il est d'une grande importance d'améliorer la qualité, la fiabilité et les performances des pièces en plastique de précision des automobiles, de réduire les coûts de production et d'améliorer l'efficacité de la production.