Co-injection is a sequential type of multi-component technology where the second component (core) is injected into the first component (skin). A specialized co-injection nozzle utilizes a pressure differential to control the ratio between the two components. This technique can reduce costs by allowing the use of less expensive core materials, such as regrind. Additionally, it can enhance part quality by incorporating a fiber-reinforced core with an unreinforced skin. By using an expanding agent in the core, sink marks can be avoided, and the required clamping force can be reduced—an additional beneficial effect.
In the packaging industry, co-injection is particularly applied in barrier injection molding. When processing polyolefins, airtight materials like EVOH are often used as a barrier layer in the core. Another unique application of co-injection is interval injection molding, which is employed to create a marbled appearance in molded parts. The repeated switching between the two components during the injection molding process results in reproducible marbling effects in parts with complex contours, while simpler contours produce tiger stripe patterns.
Co-injection molding is a specialized segment within multi-component technology.
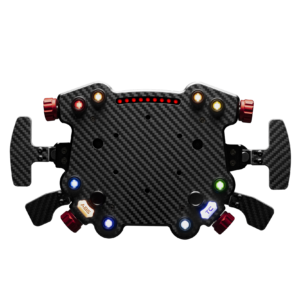
Benefits of Co-Injection:
- Cost Reduction
- Use of cheaper core materials
- Ability to utilize recycled materials
- Foamed core for lighter components
- Enhanced Part Performance
- Higher mechanical strength despite high surface quality
- Combination of galvanized skin with reinforced core
- Improved part quality—reduced sink marks