射出成形部品の場合、収縮と白化は一般的に相反する問題です。通常、部品の収縮はキャビティ圧力が低いことと部品の射出が不十分なことが原因で発生します。また、上部の白化は通常、キャビティ圧力が高いことと射出が多すぎることが原因で発生します。論理的に言えば、この2つの敵は互いに不和で、決して仲良くならないはずです。しかし、このような奇妙なことが起こりました。
金型はゲートでスプレーを発生させるため、技術者はゲートを通過させる速度を遅くします。プラスチックがランナーとゲートを通過する実際の時間は 2.8 秒で、射出時間の合計は 5.7 秒です。充填速度は非常に遅いです。
金型固定型は金型温度を使用し、実際の温度は60℃、動型は冷却水を使用し、実際の温度は28℃です。
次のことを試しました:
方法 1: 第一段階の保持圧力を高め、保持速度を速めて周辺収縮を改善し、第二段階の保持圧力を下げて上部白化問題を改善しましたが、効果はありませんでした。
方法2:射出速度の4速と5速を削除し、直接3速を使用して20mmの保持圧力切り替え点まで急速に充填し、保持圧力を高め、保持速度を遅くします。これにより、プラスチックがゆっくりと収縮し、圧力が急激に上昇しないようにしますが、効果はありません。
方法3:方法2に基づいて、可動金型の冷却水を金型温度に変更し、実際の温度は約40℃です。改善効果は明らかで、白トップや収縮はありません。成形サイクルは延長されません。
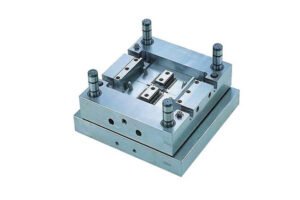
原因分析:
部品の直径は180mmですが、金型ゲートの厚さはわずか0.9mm、幅は3.5mmで、ゲートを通過する速度は非常に遅く、総充填時間は5.7秒です。また、可動金型は冷却水であり、プラスチック圧力が部品の周囲に効果的に伝達される前に、収縮および保持段階でゲートで溶融物が事前に固化します。
また、可動金型は冷却水に接続されているため、プラスチックが非常に速く冷却され、急速に収縮するプラスチックが金型コアをより大きな力で保持し、脱型が困難になります。また、可動金型の数か所にあるリブも脱型抵抗を高めます。
ゲートが薄く、充填が遅く、金型温度が比較的低いため、プラスチック圧力が大きく失われ、金型キャビティ内の圧力分布が非常に不均一になり、ゲート周辺では圧力が高く、周辺では圧力が低くなります。これらの状況が重なり合うことで、部品に収縮や白化などの比較的矛盾した欠陥が発生します。
改善策:
問題の原因が分かれば、改善策を策定するのは難しくありません。
可動金型の温度を適切に上げると、圧力損失が低減し、キャビティ圧力分布がより均一になります。これにより、ゲートの凝固時間が長くなり、プラスチック圧力が部品の周囲に効果的に伝達されるだけでなく、プラスチックの冷却速度が遅くなり、収縮保持力が低下し、脱型が容易になります。
さらに、ゲートの厚さと幅を適切に増やして(ゲートの厚さは通常、壁の厚さの 80% です)、プラスチックが通過する断面積を増やす必要があります。
もちろん、リブの抜き勾配を大きくしたり、リブを磨いたりすることも効果的です。