Hersteller von Spritzgussteilen für Gamecontroller Vor dem Formen muss der Kunststoff vollständig getrocknet sein. Wenn wasserhaltige Materialien in die Formhöhle gelangen, treten auf der Oberfläche des Produkts silberbandartige Defekte auf, und bei hohen Temperaturen kommt es sogar zu Hydrolyse, die zu Materialabbau führt. Daher muss das Material vor dem Formen vorbehandelt werden, damit es die entsprechende Feuchtigkeit behalten kann.
1. Einstellen der Formtemperatur (a) Die Formtemperatur beeinflusst den Formzyklus und die Formqualität. Im tatsächlichen Betrieb wird sie ausgehend von der niedrigsten geeigneten Formtemperatur des verwendeten Materials eingestellt und dann entsprechend dem Qualitätsstatus entsprechend angepasst. (b) Genau genommen bezieht sich die Formtemperatur auf die Temperatur der Formhohlraumoberfläche während des Formens. Bei der Gestaltung der Form und der Einstellung der Bedingungen des Formprozesses ist es nicht nur wichtig, die geeignete Temperatur beizubehalten, sondern auch dafür zu sorgen, dass sie gleichmäßig verteilt ist. (c) Eine ungleichmäßige Verteilung der Formtemperatur führt zu ungleichmäßiger Schrumpfung und innerer Spannung, wodurch die Formöffnung anfällig für Verformungen und Verwerfungen wird. (d) Eine Erhöhung der Formtemperatur kann die folgenden Effekte erzielen: 1. Erhöhung der Kristallinität und gleichmäßigere Struktur des Formprodukts. 2. Ausreichende Schrumpfung beim Formen und Verringerung der Nachschrumpfung. 3. Verbesserung der Festigkeit und Wärmebeständigkeit des Formprodukts. 4. Verringerung der restlichen inneren Spannung, der molekularen Ausrichtung und der Verformung. 5. Verringerung des Strömungswiderstands während des Füllens und Verringerung des Druckverlusts. 6. Verleiht dem Formprodukt ein glänzenderes und schöneres Aussehen. 7. Erhöht die Wahrscheinlichkeit von Graten am Formprodukt. 8. Erhöht die Wahrscheinlichkeit von Vertiefungen in der Nähe des Angusses und verringert die Wahrscheinlichkeit von Vertiefungen weiter vom Anguss entfernt. 9. Reduziert den Grad der offensichtlichen Verbindungslinie. 10. Erhöht die Abkühlzeit.
Dosierung und Plastifizierung (I) Beim Formprozess werden die Steuerung des Einspritzvolumens (Dosierung) und das gleichmäßige Schmelzen des Kunststoffs (Plastifizierung) durch die Plastifizierungseinheit der Spritzgussmaschine durchgeführt. 1. Zylindertemperatur Obwohl etwa 60–85 % des Schmelzens des Kunststoffs auf die durch die Drehung der Schnecke erzeugte Wärmeenergie zurückzuführen sind, wird der Schmelzzustand des Kunststoffs dennoch stark von der Temperatur des Zylinders beeinflusst, insbesondere von der Temperatur in der Nähe des vorderen Bereichs der Düse. Wenn die Temperatur im vorderen Bereich zu hoch ist, kann es beim Entnehmen des Produkts zu Tropfen und Gewindeschneiden kommen. 2. Schneckendrehzahl (Schneckengeschwindigkeit) (1) Das Schmelzen des Kunststoffs ist im Allgemeinen auf die durch die Drehung der Schnecke erzeugte Wärme zurückzuführen. Wenn die Schneckendrehzahl zu hoch ist, treten daher die folgenden Auswirkungen auf: 1) Thermische Zersetzung des Kunststoffs. 2) Verkürzung der Glasfaser (faserverstärkter Kunststoff). Beschleunigter Verschleiß der Schnecke oder des Zylinders. (2) Die Einstellung der Rotationsgeschwindigkeit kann anhand der Größe der Umfangsgeschwindigkeit der Schnecke gemessen werden: Umfangsgeschwindigkeit = n (Rotationsgeschwindigkeit) * d (Durchmesser) * π (Pi). Normalerweise kann die Umfangsgeschwindigkeit der Schneckenstange bei Kunststoffen mit niedriger Viskosität und guter thermischer Stabilität auf etwa 1 m/s eingestellt werden, bei Kunststoffen mit geringer thermischer Stabilität sollte sie jedoch nur etwa 0,1 betragen. (3) In praktischen Anwendungen können wir versuchen, die Schneckengeschwindigkeit zu senken, sodass die Rotationszufuhr vor dem Öffnen der Form abgeschlossen sein kann.
3. Gegendruck (GEGENDRUCK) (1) Wenn sich die Schnecke dreht, um zuzuführen, wird der Druck, der durch das geschmolzene Plastik entsteht, das an das vordere Ende der Schnecke gedrückt wird, als Gegendruck bezeichnet. Während des Spritzgießens kann er durch Einstellen des Öldrucks des hydraulischen Spritzzylinders angepasst werden. Gegendruck kann folgende Auswirkungen haben: 1) Das geschmolzene Plastik wird gleichmäßiger geschmolzen. 2) Farb- und Füllstoffe werden gleichmäßiger verteilt. 3) Das Gas wird aus der Verschlussöffnung abgelassen. 4) Die Zufuhr wird genau gemessen. (2) Der Gegendruck wird durch die Viskosität des Plastiks und seine thermische Stabilität bestimmt. Ein zu hoher Gegendruck verzögert die Zufuhrzeit und erhöht die Rotationsscherkraft, was zu einer Überhitzung des Plastiks führen kann. Im Allgemeinen sind 5 bis 15 kg/cm² angemessen.
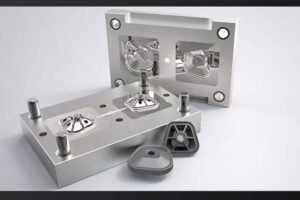
4. Rücksaugen (Dekompression) (1) Nachdem sich die Stange dreht und vorschiebt, wird die Schraube richtig zurückgezogen, um den Druck des geschmolzenen Kunststoffs am vorderen Ende der Schraube zu verringern. Dies wird als Rücksaugen bezeichnet und kann ein Tropfen aus der Düse verhindern. (2) Unzureichender Gegendruck kann dazu führen, dass der Hauptkanal (SPRUE) an der Form festklebt; zu hoher Gegendruck kann Luft einsaugen und Luftflecken auf dem geformten Produkt verursachen.
Einstellen der Anzahl stabiler Formteile (I) Vorbestätigung und vorbereitende Einstellungen 1. Bestätigen Sie, dass Materialtrocknung, Formtemperatur und Heizrohrtemperatur richtig eingestellt sind und den verarbeitbaren Zustand erreicht haben. 2. Überprüfen Sie die Aktion und die Distanzeinstellung für das Öffnen und Schließen der Form und das Auswerfen. 3. Der Einspritzdruck (P1) ist auf 60% des Maximalwerts eingestellt. 4. Stellen Sie den Haltedruck (PH) auf 30% des Maximalwerts ein. 5. Stellen Sie die Einspritzgeschwindigkeit (V1) auf 40% des Maximalwerts ein. 6. Stellen Sie die Schneckengeschwindigkeit (VS) auf etwa 60 U/min ein. 7. Stellen Sie den Gegendruck (PB) auf etwa 10 kg/cm² ein. 8. Stellen Sie den Gegendruck auf etwa 3 mm ein. 9. Stellen Sie die Position des Haltedruckschalters auf 30% des Schneckendurchmessers ein. Stellen Sie ihn beispielsweise für eine Schnecke mit φ100 mm auf 30 mm ein. 10. Stellen Sie den Dosierhub etwas kürzer als den berechneten Wert ein. 11. Stellen Sie die Gesamteinspritzzeit etwas kürzer und die Abkühlzeit etwas länger ein. (II) Korrektur der manuellen Betriebsparameter 1. Verriegeln Sie die Form (bestätigen Sie den Anstieg des hohen Drucks) und der Einspritzsitz bewegt sich nach vorne. 2. Injizieren Sie manuell, bis die Schraube vollständig stoppt und achten Sie auf die Stoppposition. 3. Die Schraube dreht sich zurück, um zuzuführen. 4. Öffnen Sie nach dem Abkühlen die Form und nehmen Sie das geformte Produkt heraus. 5. Wiederholen Sie die Schritte ⑴~⑷ und die Schraube wird schließlich bei einer Position von 10%~20% des Schraubendurchmessers stoppen und das geformte Produkt wird keine kurzen Schüsse, Grate, Weißfärbungen oder Risse aufweisen. (III) Korrektur der Parameter für den halbautomatischen Betrieb 1. Korrektur des Dosierhubs [Dosierendpunkt] Erhöhen Sie den Einspritzdruck auf 99%, stellen Sie den Haltedruck vorübergehend auf 0 ein, verstellen Sie den Dosierendpunkt S0 nach vorne, bis ein kurzer Schuss auftritt, und verstellen Sie ihn dann nach hinten, bis ein Grat auftritt, und verwenden Sie den Mittelpunkt als ausgewählte Position. 2. Korrektur der Einspritzgeschwindigkeit Bringen Sie PH auf den ursprünglichen Wert zurück, passen Sie die Einspritzgeschwindigkeit nach oben und unten an, ermitteln Sie die einzelnen Geschwindigkeiten, bei denen kurze Schüsse und Grate auftreten, und verwenden Sie den Mittelpunkt als entsprechende Geschwindigkeit [in diesem Stadium können Sie auch die Parametereinstellung der Mehrfachgeschwindigkeit entsprechend den Erscheinungsproblemen eingeben]. 3. Korrektur des Haltedrucks Passen Sie den Haltedruck nach oben und unten an, ermitteln Sie die einzelnen Drücke, bei denen Oberflächenvertiefungen und Grate auftreten, und verwenden Sie den Mittelpunkt als ausgewählten Haltedruck. 4. Korrektur der Haltezeit [oder Einspritzzeit] Verlängern Sie die Haltezeit schrittweise, bis das Gewicht des geformten Produkts offensichtlich stabil ist, was eine klare und angemessene Wahl ist 5. Korrektur der Abkühlzeit Reduzieren Sie die Abkühlzeit schrittweise und vergewissern Sie sich, dass die folgenden Bedingungen erfüllt werden können: (1) Das geformte Produkt wird beim Auswerfen, Festklemmen, Beschneiden oder Verpacken nicht weißlich, konvex oder verformt. (2) Die Formtemperatur kann ausgeglichen und stabil sein. Einfache Berechnungsmethode für die Abkühlzeit von Produkten mit einer Wandstärke von über 4 mm: 1) Theoretische Abkühlzeit = S (1 + 2S) Formtemperatur unter 60 Grad. (2) Theoretische Abkühlzeit = 1,3S (1 + 2S) … Formtemperatur über 60 Grad [S steht für die maximale Wandstärke des geformten Produkts]. 6. Korrektur der Plastifizierungsparameter (1) Vergewissern Sie sich, ob der Gegendruck angepasst werden muss. (2) Passen Sie die Schneckengeschwindigkeit so an, dass die Dosierzeit etwas kürzer als die Abkühlzeit ist. (3) Vergewissern Sie sich, dass die Dosierzeit stabil ist, und versuchen Sie, den Gradienten der Heizspulentemperatur anzupassen. (4) Überprüfen Sie, ob aus der Düse tropft, ob sich ein Pigtail oder ein Feststecken im Hauptkanal befindet und ob sich Luftflecken auf dem fertigen Produkt befinden, und passen Sie die Düsentemperatur oder den Lockerungsabstand entsprechend an. 7. Verwendung von abgestuftem Haltedruck und mehrstufiger Einspritzgeschwindigkeit (1) Im Allgemeinen sollte das Einspritzen mit hoher Geschwindigkeit erfolgen, ohne das Erscheinungsbild zu beeinträchtigen, aber beim Durchlaufen des Angusses und vor dem Umschalten auf Haltedruck sollte die Geschwindigkeit verringert werden; (2) Der Haltedruck sollte schrittweise verringert werden, um übermäßige Restspannungen im Formprodukt zu vermeiden, die dazu führen können, dass sich das Formprodukt leicht verformt.