Производитель игровых контроллеров для литья под давлением Перед формованием пластик должен быть полностью высушен. При попадании в полость формы материалов, содержащих воду, на поверхности изделия появятся дефекты в виде серебристой ленты, а при высоких температурах даже произойдет гидролиз, вызывающий деградацию материала. Поэтому перед формованием материал необходимо предварительно обработать, чтобы он мог сохранять соответствующую влажность.
1. Установка температуры пресс-формы (a) Температура пресс-формы влияет на цикл формования и качество формования. В реальной работе она устанавливается на основе самой низкой подходящей температуры пресс-формы используемого материала, а затем соответствующим образом регулируется в соответствии с состоянием качества. (b) Правильно говоря, температура пресс-формы относится к температуре поверхности полости пресс-формы при выполнении формования. При проектировании пресс-формы и установке условий процесса формования важно не только поддерживать соответствующую температуру, но и равномерно ее распределять. (c) Неравномерное распределение температуры пресс-формы приведет к неравномерной усадке и внутреннему напряжению, что делает формовочный порт склонным к деформации и короблению. (d) Повышение температуры пресс-формы может достичь следующих эффектов: 1. Увеличить кристалличность и более однородную структуру формованного изделия. 2. Сделать усадку формования более достаточной и уменьшить пост-усадку. 3. Улучшить прочность и термостойкость формованного изделия. 4. Уменьшить остаточное внутреннее напряжение, молекулярную ориентацию и деформацию. 5. Уменьшить сопротивление потоку во время заполнения и уменьшить потерю давления. 6. Сделать внешний вид формованного изделия более блестящим и качественным. 7. Увеличить вероятность появления заусенцев на формованном изделии. 8. Увеличить вероятность появления вмятин вблизи литника и уменьшить вероятность появления вмятин вдали от литника. 9. Уменьшить степень очевидной линии склеивания. 10. Увеличить время охлаждения.
Дозирование и пластификация (I) В процессе формования контроль объема впрыска (дозирование) и равномерное плавление пластика (пластификация) выполняются пластифицирующим узлом литьевой машины. 1. Температура цилиндра Хотя около 60~85% плавления пластика происходит из-за тепловой энергии, вырабатываемой вращением шнека, состояние плавления пластика по-прежнему сильно зависит от температуры цилиндра, особенно температуры вблизи передней области сопла. Когда температура передней области слишком высока, вероятно возникновение капания и налипания при извлечении продукта. 2. Скорость шнека (скорость шнека) (1) Плавление пластика, как правило, происходит из-за тепла, вырабатываемого вращением шнека. Поэтому, если скорость шнека слишком высокая, произойдут следующие эффекты: 1) Термическое разложение пластика. 2) Укорочение стекловолокна (армированного волокном пластика). Ускоренный износ шнека или цилиндра. (2) Установка скорости вращения может быть измерена по величине окружной скорости его шнека: Окружная скорость = n (скорость вращения) * d (диаметр) * π (пи) Обычно для пластиков с низкой вязкостью и хорошей термической стабильностью окружная скорость стержня шнека может быть установлена на уровне около 1 м/с, но для пластиков с плохой термической стабильностью она должна быть всего лишь около 0,1. (3) На практике мы можем попытаться снизить скорость шнека, чтобы вращательная подача могла быть завершена до открытия формы.
3. Обратное давление (ОБРАТНОЕ ДАВЛЕНИЕ) (1) Когда шнек вращается для подачи, давление, накопленное расплавленным пластиком, выталкиваемым к переднему концу шнека, называется обратным давлением. Во время литья под давлением его можно регулировать, регулируя давление масла в гидравлическом цилиндре впрыска. Обратное давление может иметь следующие эффекты: 1) Расплавленный пластик плавится более равномерно. 2) Краситель и наполнитель распределяются более равномерно. 3) Газ выпускается из отверстия для заглушки. 4) Подача точно измеряется. (2) Обратное давление определяется вязкостью пластика и его термической стабильностью. Слишком высокое обратное давление задержит время подачи и увеличит вращательное усилие сдвига, что может привести к перегреву пластика. Обычно подходит 5~15 кг/см2.
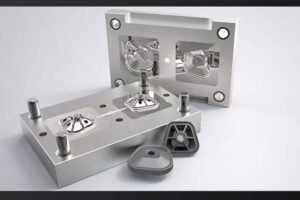
4. Обратное всасывание (декомпрессия) (1) После вращения и подачи стержня шнек надлежащим образом отводится для снижения давления расплавленного пластика на переднем конце шнека. Это называется обратным всасыванием, которое может предотвратить капание из сопла. (2) Недостаточное обратное давление может привести к прилипанию основного канала (SPRUE) к форме; слишком большое обратное давление может привести к всасыванию воздуха и появлению воздушных следов на формованном изделии.
Установка количества стабильных формовок (I) Предварительное подтверждение и подготовительные настройки 1. Убедитесь, что сушка материала, температура формы и температура нагревательной трубки установлены правильно и достигли обрабатываемого состояния. 2. Проверьте действие и настройку расстояния открытия и закрытия формы и выброса. 3. Давление впрыска (P1) установлено на 60% от максимального значения. 4. Установите давление выдержки (PH) на 30% от максимального значения. 5. Установите скорость впрыска (V1) на 40% от максимального значения. 6. Установите скорость шнека (VS) примерно на 60 об/мин. 7. Установите обратное давление (PB) примерно на 10 кг/см2. 8. Установите обратное давление примерно на 3 мм. 9. Установите положение переключателя давления выдержки на 30% от диаметра шнека. Например, для шнека φ100 мм установите его на 30 мм. 10. Установите ход дозирования немного короче расчетного значения. 11. Установите общее время впрыска немного короче, а время охлаждения немного длиннее. (II) Корректировка параметров ручного управления 1. Заблокируйте форму (подтвердите рост высокого давления), и седло впрыска переместится вперед. 2. Впрыскивайте вручную до полной остановки шнека и обратите внимание на положение остановки. 3. Шнек вращается обратно для подачи. 4. После охлаждения откройте форму и выньте формованное изделие. 5. Повторите шаги ⑴~⑷, и шнек в конечном итоге остановится в положении 10%~20% диаметра шнека, и формованное изделие не будет иметь недостаточных выстрелов, заусенцев, побеления или трещин. (III) Коррекция параметров полуавтоматической работы 1. Коррекция хода дозирования [конечная точка дозирования] Увеличьте давление впрыска до 99% и временно отрегулируйте давление удержания до 0, отрегулируйте конечную точку дозирования S0 вперед, пока не произойдет короткий выстрел, а затем отрегулируйте ее назад, пока не произойдет заусенец, и используйте среднюю точку в качестве выбранного положения. 2. Коррекция скорости впрыска Верните PH на исходный уровень, отрегулируйте скорость впрыска вверх и вниз, выясните отдельные скорости, при которых происходят короткие выстрелы и заусенцы, и используйте среднюю точку в качестве соответствующей скорости [на этом этапе вы также можете ввести настройку параметров многоскоростного режима, соответствующую проблемам внешнего вида]. 3. Коррекция давления удержания Отрегулируйте давление удержания вверх и вниз, выясните отдельные давления, при которых возникают поверхностные углубления и заусенцы, и используйте среднюю точку в качестве выбранного давления удержания. 4. Коррекция времени удержания [или времени впрыска] Постепенно увеличивайте время удержания, пока вес отформованного изделия не станет явно стабильным, что является ясным и правильным выбором. 5. Корректировка времени охлаждения Постепенно уменьшайте время охлаждения и убедитесь, что могут быть выполнены следующие условия: (1) Формованное изделие не будет белеть, выпуклым или деформироваться при выталкивании, зажиме, обрезке или упаковке. (2) Температура формы может быть сбалансированной и стабильной. Простой метод расчета времени охлаждения изделий с толщиной стенки более 4 мм: 1) Теоретическое время охлаждения = S (1 + 2S) температура формы ниже 60 градусов. (2) Теоретическое время охлаждения = 1,3S (1 + 2S) …. температура формы выше 60 градусов [S представляет максимальную толщину стенки формованного изделия]. 6. Корректировка параметров пластификации (1) Подтвердите, нужно ли регулировать противодавление; (2) Отрегулируйте скорость шнека так, чтобы время дозирования было немного короче времени охлаждения; (3) Подтвердите, стабильно ли время дозирования, и попробуйте отрегулировать градиент температуры нагревательной спирали. (4) Убедитесь, что из сопла не капает, нет ли косичек или застреваний в основном канале, а также нет ли воздушных следов на готовом изделии, и соответствующим образом отрегулируйте температуру сопла или расстояние ослабления. 7. Использование ступенчатого давления выдержки и многоступенчатой скорости впрыска (1) Как правило, впрыск следует выполнять на высокой скорости, не влияя на внешний вид, но его следует выполнять на более низкой скорости при прохождении через литник и перед переключением на давление выдержки; (2) Давление выдержки следует постепенно снижать, чтобы избежать чрезмерного остаточного напряжения в формованном изделии, которое может привести к его легкой деформации.