Fabricante de moldes de inyección para controladores de juegos Antes de moldearlo, el plástico debe secarse por completo. Cuando los materiales que contienen agua ingresan a la cavidad del molde, aparecerán defectos en forma de cinta plateada en la superficie del producto e incluso se producirá hidrólisis a altas temperaturas, lo que provocará la degradación del material. Por lo tanto, el material debe tratarse previamente antes del moldeo para que pueda mantener la humedad adecuada.
1. Ajuste de la temperatura del molde (a) La temperatura del molde afecta el ciclo de moldeo y la calidad del moldeo. En la operación real, se establece a partir de la temperatura de molde adecuada más baja del material utilizado y luego se ajusta adecuadamente de acuerdo con el estado de calidad. (b) Hablando correctamente, la temperatura del molde se refiere a la temperatura de la superficie de la cavidad del molde cuando se lleva a cabo el moldeo. En el diseño del molde y el ajuste de la condición del proceso de moldeo, es importante no solo mantener la temperatura adecuada, sino también distribuirla uniformemente. (c) La distribución desigual de la temperatura del molde provocará una contracción desigual y una tensión interna, lo que hace que el puerto de moldeo sea propenso a deformarse y deformarse. (d) El aumento de la temperatura del molde puede lograr los siguientes efectos; 1. Aumentar la cristalinidad y una estructura más uniforme del producto moldeado. 2. Hacer que la contracción del moldeo sea más suficiente y reducir la contracción posterior. 3. Mejorar la resistencia y la resistencia al calor del producto moldeado. 4. Reducir la tensión interna residual, la orientación molecular y la deformación. 5. Reducir la resistencia al flujo durante el llenado y reducir la pérdida de presión. 6. Hacer que la apariencia del producto moldeado sea más brillante y buena. 7. Aumentar la posibilidad de rebabas en el producto moldeado. 8. Aumentar la posibilidad de depresión cerca de la compuerta y reducir la posibilidad de depresión lejos de la compuerta. 9. Reducir el grado de línea de unión obvia 10. Aumentar el tiempo de enfriamiento.
Dosificación y plastificación (I) En el proceso de moldeo, el control del volumen de inyección (dosificación) y la fusión uniforme del plástico (plastificación) se realizan mediante la unidad de plastificación de la máquina de moldeo por inyección. 1. Temperatura del barril Aunque alrededor del 60 ~ 85% de la fusión del plástico se debe a la energía térmica generada por la rotación del tornillo, el estado de fusión del plástico todavía se ve muy afectado por la temperatura del barril, especialmente la temperatura cerca del área frontal de la boquilla. Cuando la temperatura del área frontal es demasiado alta, es probable que se produzcan goteos y roscas al retirar el producto. 2. Velocidad del tornillo (velocidad del tornillo) (1) La fusión del plástico generalmente se debe al calor generado por la rotación del tornillo. Por lo tanto, si la velocidad del tornillo es demasiado rápida, se producirán los siguientes efectos: 1) Descomposición térmica del plástico. 2) Acortamiento de la fibra de vidrio (plástico reforzado con fibra). Desgaste acelerado del tornillo o barril. (2) El ajuste de la velocidad de rotación se puede medir por el tamaño de su velocidad circunferencial del tornillo: Velocidad circunferencial = n (velocidad de rotación) * d (diámetro) * π (pi) Por lo general, para plásticos con baja viscosidad y buena estabilidad térmica, la velocidad circunferencial de la varilla del tornillo se puede establecer en aproximadamente 1 m/s, pero para plásticos con poca estabilidad térmica, debe ser tan baja como aproximadamente 0,1. (3) En aplicaciones prácticas, podemos intentar reducir la velocidad del tornillo para que la alimentación rotatoria se pueda completar antes de abrir el molde.
3. Contrapresión (CONTRAPRESIÓN) (1) Cuando el tornillo gira para alimentar, la presión acumulada por el plástico fundido empujado hacia el extremo delantero del tornillo se llama contrapresión. Durante el moldeo por inyección, se puede ajustar ajustando la presión de aceite del cilindro hidráulico de inyección. La contrapresión puede tener los siguientes efectos: 1) El plástico fundido se funde de manera más uniforme. 2) El colorante y el relleno se dispersan de manera más uniforme. 3) El gas se descarga desde el puerto de obturación. 4) La alimentación se mide con precisión. (2) La contrapresión está determinada por la viscosidad del plástico y su estabilidad térmica. Una contrapresión demasiado alta retrasará el tiempo de alimentación y aumentará la fuerza de corte rotacional, lo que puede provocar que el plástico se sobrecaliente. Generalmente, 5~15 kg/cm2 es apropiado.
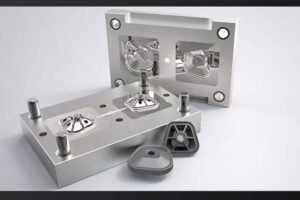
4. Succión hacia atrás (descompresión) (1) Después de que la varilla gira y se alimenta, el tornillo se retira adecuadamente para reducir la presión del plástico fundido en el extremo delantero del tornillo. Esto se llama succión hacia atrás, que puede evitar el goteo de la boquilla. (2) Una contrapresión insuficiente puede hacer que el canal principal (SPRUE) se adhiera al molde; una contrapresión excesiva puede inhalar aire y causar marcas de aire en el producto moldeado.
Ajuste del número de moldeo estable (I) Ajustes previos a la confirmación y preparatorios 1. Confirme si el secado del material, la temperatura del molde y la temperatura del tubo de calentamiento están configurados correctamente y alcanzan el estado procesable. 2. Verifique la acción y el ajuste de la distancia de apertura y cierre del molde y expulsión. 3. La presión de inyección (P1) se establece en 60% del valor máximo. 4. Establezca la presión de retención (PH) en 30% del valor máximo. 5. Establezca la velocidad de inyección (V1) en 40% del valor máximo. 6. Establezca la velocidad del tornillo (VS) en aproximadamente 60 RPM. 7. Establezca la contrapresión (PB) en aproximadamente 10 kg/cm2. 8. Establezca la contrapresión en aproximadamente 3 mm. 9. Establezca la posición del interruptor de presión de retención en 30% del diámetro del tornillo. Por ejemplo, para un tornillo de φ100 mm, configúrelo en 30 mm. 10. Ajuste la carrera de dosificación ligeramente más corta que el valor calculado. 11. Ajuste el tiempo total de inyección ligeramente más corto y el tiempo de enfriamiento ligeramente más largo. (II) Corrección de parámetros de operación manual 1. Bloquee el molde (confirme el aumento de alta presión), y el asiento de inyección se mueve hacia adelante. 2. Inyecte manualmente hasta que el tornillo se detenga por completo y preste atención a la posición de parada. 3. El tornillo gira de nuevo para alimentar. 4. Después de enfriar, abra el molde y saque el producto moldeado. 5. Repita los pasos ⑴~⑷, y el tornillo finalmente se detendrá en una posición de 10%~20% del diámetro del tornillo, y el producto moldeado no tendrá disparos cortos, rebabas, blanqueamiento o grietas. (III) Corrección de los parámetros de funcionamiento semiautomático 1. Corrección de la carrera de dosificación [punto final de dosificación] Aumente la presión de inyección a 99% y ajuste temporalmente la presión de retención a 0, ajuste el punto final de dosificación S0 hacia adelante hasta que se produzca un disparo corto y luego ajústelo hacia atrás hasta que se produzca una rebaba y utilice el punto medio como la posición seleccionada. 2. Corrección de la velocidad de inyección Regrese PH al nivel original, ajuste la velocidad de inyección hacia arriba y hacia abajo, descubra las velocidades individuales donde se producen disparos cortos y rebabas, y utilice el punto medio como la velocidad adecuada [en esta etapa, también puede ingresar la configuración de parámetros de velocidad múltiple correspondiente a problemas de apariencia]. 3. Corrección de la presión de retención Ajuste la presión de retención hacia arriba y hacia abajo, descubra las presiones individuales donde se producen depresiones superficiales y rebabas, y utilice el punto medio como la presión de retención seleccionada. 4. Corrección del tiempo de retención [o tiempo de inyección] Amplíe gradualmente el tiempo de retención hasta que el peso del producto moldeado sea obviamente estable, lo cual es una opción clara y apropiada. 5. Corrección del tiempo de enfriamiento Reduzca gradualmente el tiempo de enfriamiento y confirme que se pueden cumplir las siguientes condiciones: (1) El producto moldeado no se blanqueará, convexo ni deformará al ser expulsado, sujetado, recortado o empaquetado. (2) La temperatura del molde puede equilibrarse y estabilizarse. Método de cálculo simple para el tiempo de enfriamiento de productos con un espesor de pared de más de 4 mm: 1) Tiempo de enfriamiento teórico = S (1 + 2S) temperatura del molde por debajo de 60 grados. (2) Tiempo de enfriamiento teórico = 1.3S (1 + 2S) …. temperatura del molde por encima de 60 grados [S representa el espesor máximo de pared del producto moldeado]. 6. Corrección de los parámetros de plastificación (1) Confirme si es necesario ajustar la contrapresión; (2) Ajuste la velocidad del tornillo para que el tiempo de dosificación sea ligeramente más corto que el tiempo de enfriamiento; (3) Confirme si el tiempo de dosificación es estable e intente ajustar el gradiente de la temperatura de la bobina de calentamiento. (4) Confirme si hay goteo de la boquilla, si hay una coleta o atascos en el canal principal, y si hay marcas de aire en el producto terminado, y ajuste la temperatura de la boquilla o la distancia de aflojamiento de manera apropiada. 7. Utilización de presión de retención por etapas y velocidad de inyección de múltiples etapas (1) En términos generales, la inyección debe realizarse a alta velocidad sin afectar la apariencia, pero debe realizarse a una velocidad más baja al pasar por la compuerta y antes de cambiar a presión de retención; (2) La presión de retención debe reducirse gradualmente para evitar una tensión residual excesiva en el producto moldeado, que puede hacer que el producto moldeado se deforme fácilmente.